Since its very first integration into various business processes, the Internet of Things has been known for its potential to streamline the manufacturing industry. There are numerous digital transformation possibilities related to IoT in manufacturing – from sensors and wearable devices to cloud software.
The adoption levels are so substantial, that McKinsey even predicts the economic impact of the Internet of Things in manufacturing to be as high as $3.7 trillion by 2025. If you’re intrigued, let’s delve into five extremely smart and promising IoT solutions for manufacturing that you can potentially use for your business.
1. Keep Production Uninterrupted with Predictive Maintenance
With this manufacturing IoT solution, there’s no need to repeatedly interrupt the production process to manually scan for potential defects or irregularities in the manufacturing equipment anymore. Predictive maintenance in the form of embedded devices and sensors in the machinery can continuously monitor the performance and alert operators when the anomaly triggers the pre-set indicators and parameters.
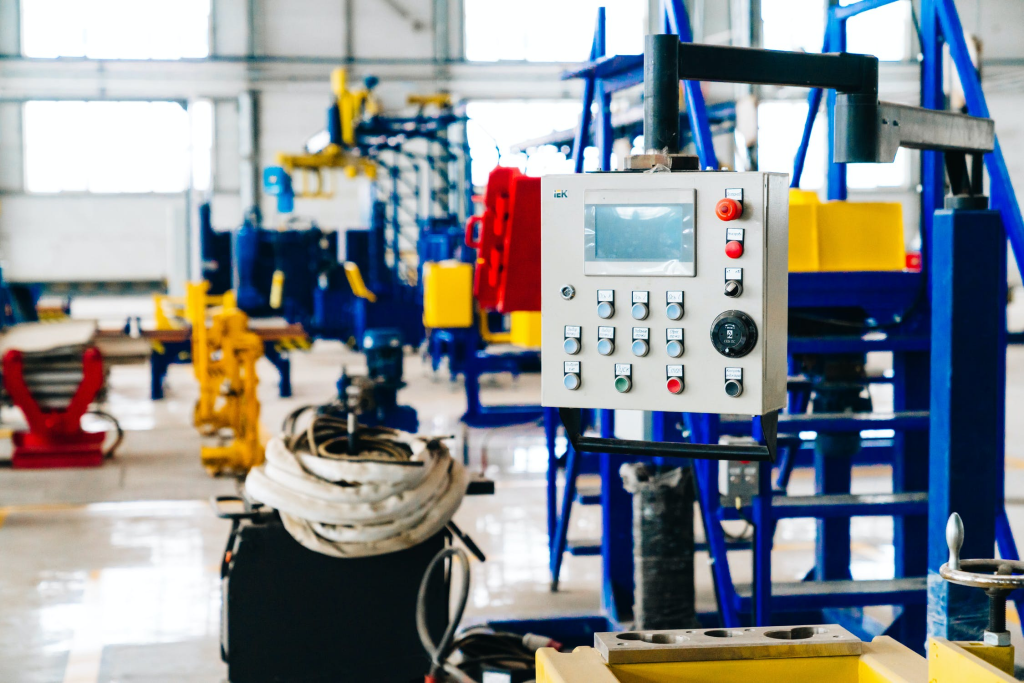
The potential anomalies can be either faulty components, equipment deterioration, rapid temperature drops or rises, pressure and vibration fluctuations, or voltage abnormalities. Without timely detection, these flaws can result in serious and quite costly damage that cannot be quickly repaired especially when dealing with sensitive materials.
This IoT manufacturing tool can also help with technical support anticipation and automated supervision if you directly integrate devices connected to the Internet of Things with advanced data analysis software or AI. You can also connect these devices to similar manufacturing devices, old systems, IFTTT programs, or Cloud Application Programming Interfaces.
Besides reducing maintenance costs, predictive or conditions based maintenance can increase the service life of parts and reduce the need for a large stock of spare ones, as well as boost efficiency by reducing the inactive periods in manufacturing due to repairs and minimize the production delays.
2. Improve Process Efficiency with Real-Time Asset Tracking
Next in our list of Internet of Things manufacturing examples comes real-time asset tracking. In this case, the Internet of Things seamlessly blends into native or web applications during development to enable comprehensive asset monitoring and process visibility.
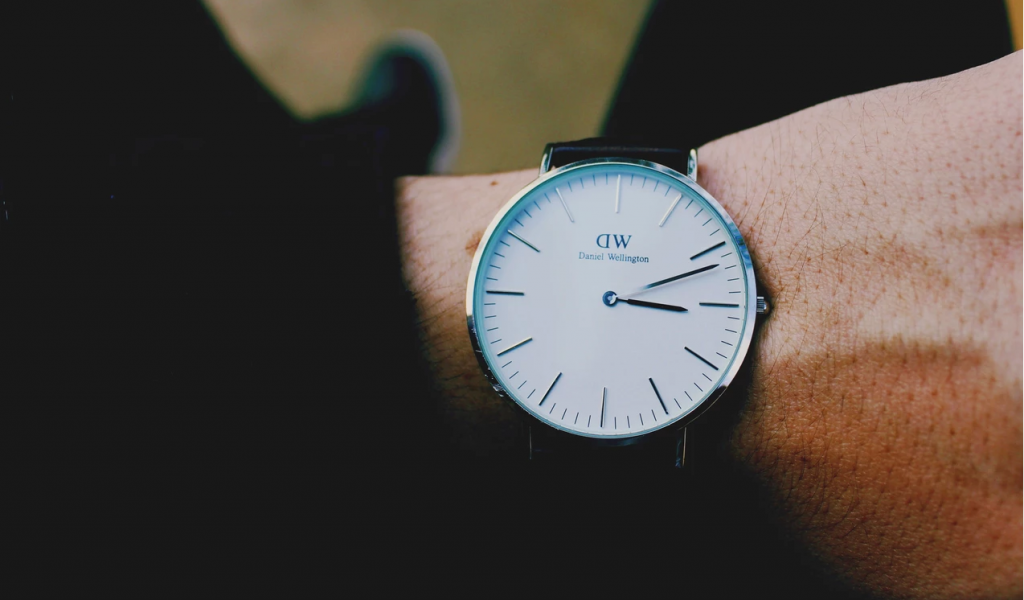
Multiple tracking devices are being attached to the moving equipment to follow every single move they’re making across the facility. IoT trackers work with almost any type of operating equipment – containers, inventory, carts, rolling stocks, small tools, and even workers. Received data can be presented in reports, diagrams, or key performance indicators.
Manufacturers can then keep an eye on all their assets’ locations and conditions and control the product’s lifecycle to increase efficiency in everything, including task assignment. You can detect unusual and inefficient routes or inactive equipment. Besides, by adding AI or machine learning to this IoT in manufacturing, you can transform asset management to further automate existing workflows, up to the final product delivery.
The efficiency upgrade mainly comes from the thorough supervising and organization of the supply chain and all its elements, which is particularly doable with asset tracking. By receiving real-time alerts, data, and important insights, companies can optimize their logistics, monitor their stocks, discover and predict fraudulent behavior from partners or employees.
3. Monitor WIP with Asset Tracking
With the same manufacturing Internet of Things tracking solution, you can monitor and optimize the Work-in-Progress system’s movements as well. This can help identify inefficiencies and avoid excesses in numerous parts of the manufacturing process. For example, too much inventory of parts can essentially lead to slower performance down the line, or even worse, cause overproduction.
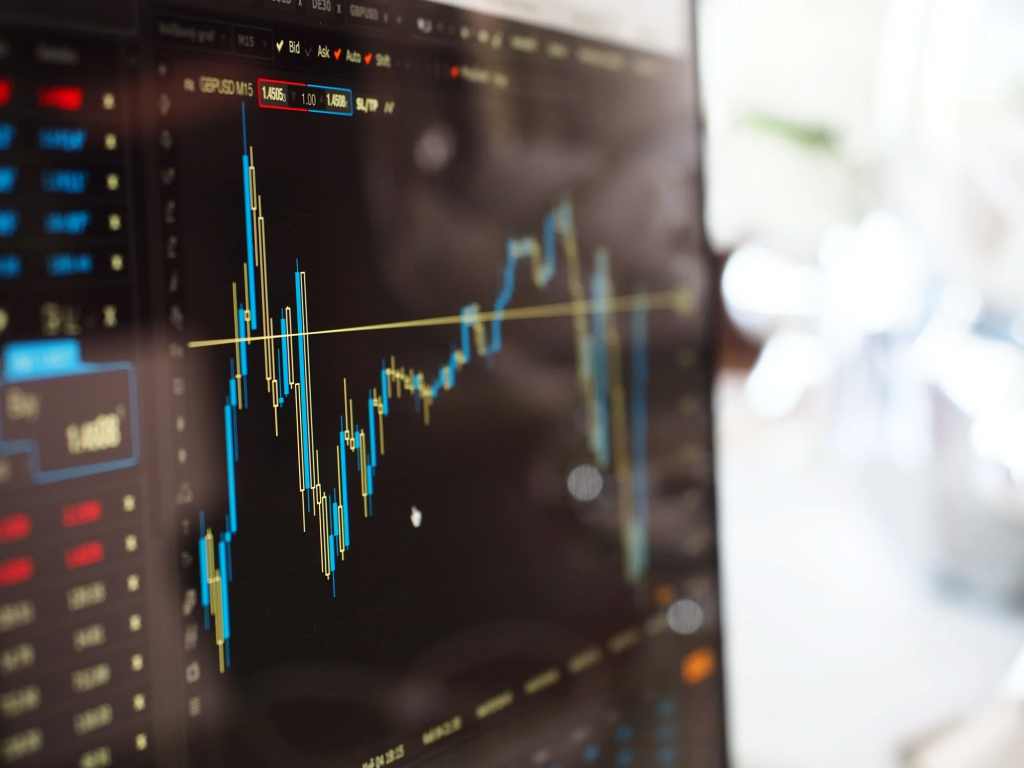
Usually, when the manufacturing process is stable enough, there’s little to no overproduction due to highly organized production flow. There can be limited variations in the process, but nothing too overboard. However, if multiple errors and lapses in judgment stack on each other, there’s a higher chance of making a lot more products than required, which is often called the most hazardous type of waste in manufacturing.
Asset tracking can make sure this doesn’t happen. To efficiently track the progress of WIP and oversee the application of all available, companies need consistent and already proved information. The IoT in manufacturing solution called real-time location systems (RTLS) is able to make the manufacturing process more predictable and manageable.
RTLS is usually a mixture of both software and hardware. Analytical software helps visualize and present the collected data, while location tags and services that connect all IT systems gather and adapt the data flow.
4. Improve Employee Engagement with Real-Time Tracking
Real-time tracking IoT in manufacturing can also aid in improving employee engagement. This time, the tracking software is focused solely on employees and their performance on the production floor. While it may seem like a violation of trust and personal boundaries, usually, it’s not. When done correctly, RTLS is extra helpful in analyzing work achievements and continuous performance and productivity for better management.
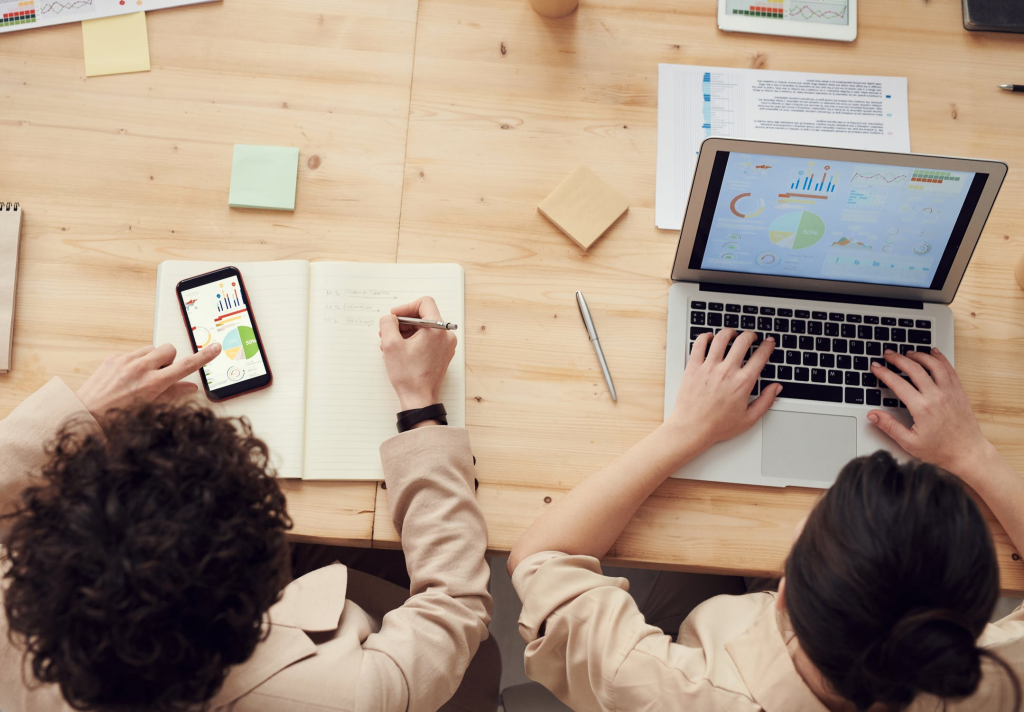
Sometimes, when a few workers start performing poorly and fall behind on the schedule, it can set back the whole production. Such a decrease in operational efficiency can easily be avoided with the Internet of Things manufacturing tracking software. Besides predicting the slowdown periods in manufacturing, real-time tracking can also help further improve productivity by focusing on each worker and their individual styles, avoid churn, and lower the business costs.
Employee tracking generally involves monitoring the workers’ time in specific areas and analyzing standard movement across the facility for more accurate task assignments. It may include light, pretty unnoticeable easy-to-wear tags that won’t hinder the person’s range of motion. These tags can also be used as card keys to grant and track access to different parts of the production and warehouses in real-time for faster employee location.
5. Enhance Safety and Compliance with IoT Sensors
The last combination of IoT and manufacturing in our list are IoT devices used for accident prevention. These devices range from standard sensors and cameras to thermostats or even door locks. It may seem that accidents in the workplace are not that common and are usually caused by negligence or ignorance.
In reality, even the slightest hardware malfunction can potentially be hazardous. As claimed by the National Safety Council, every seven seconds there’s a work injury in the USA, which comes to 4.7 million injured employees per year. Even something seemingly harmless as an email can serve as a distraction and carelessness or loss of focus would ensue.
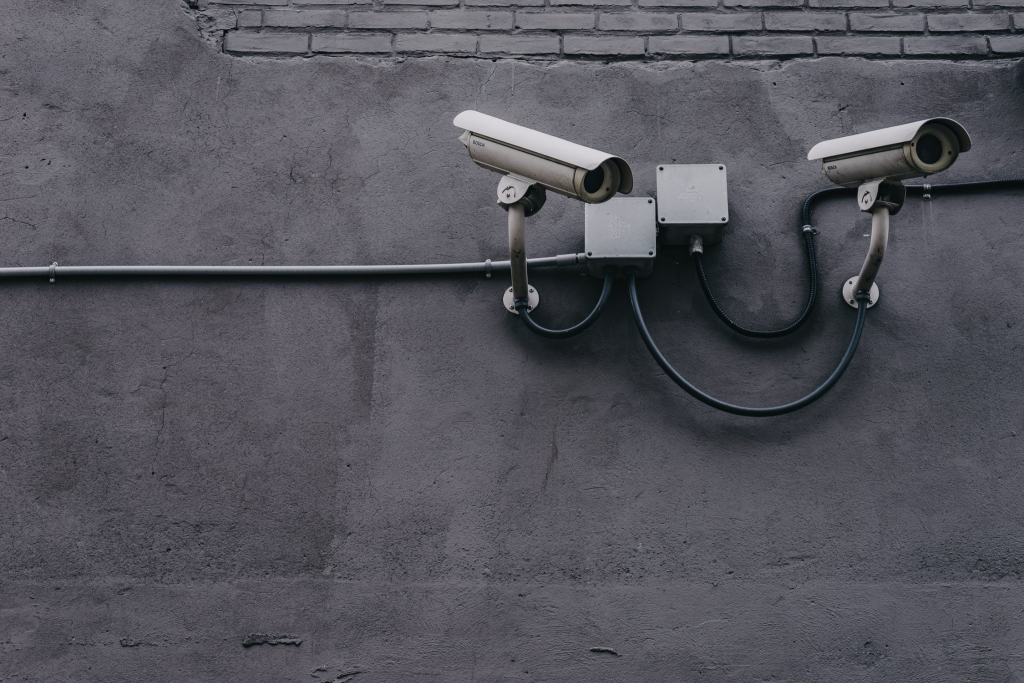
The embedded IoT for manufacturing purposes can scan every available equipment for potential risks to workers’ health and wellbeing. Being proactive and not reactive can save many lives and subsequently lower the compensation expenses that will surely be better off spent on salaries, new equipment, and software upgrades.
It even came to such wearable IoT innovations that can monitor the employee’s health and alert of the sudden changes in pressure, temperature, heart rate, or blood oxygen to prevent fatigue or more serious diseases. It can be useful while working with potentially unsafe materials, unstable conditions, or harsh and unusual environments.
Summary
Out of all major industries, the integration of the currently trending Internet of Things into manufacturing infrastructure seemed inevitable to begin with. IoT in manufacturing presents a wide variety of opportunities for production optimization, more agile organization of the company’s internal processes, cost reduction, and many other benefits. If you’d like to learn more and potentially integrate IoT into your business, feel free to reach out.