The global supply chain landscape has undergone massive shifts over the past few years, revealing vulnerabilities and challenges across industries. Namely, businesses and organizations are scrambling to optimize their supply chains, from disruptions caused by geopolitical events and pandemics to rising costs and sustainability concerns.
Let’s take a look at some initial stats:
- A study by the Capgemini Research Institute reported that 57% of organizations believe their supply chains need a complete overhaul in response to these challenges. And a McKinsey report says that 92% of executives have made significant changes to their supply chains over the past year in response to these disruptions.
- Furthermore, the global supply chain market is expected to grow from $15.85 billion in 2021 to $31 billion by 2026, highlighting the urgency for businesses to adapt and innovate timely. But we have more essential stats for you to explore.
In this article, we’ll go through the key challenges facing supply chain management today, the technology trends reshaping the field, and the solutions organizations can implement to streamline operations and prepare for the future — all backed up with proper statistics.
Challenges in Supply Chain Management
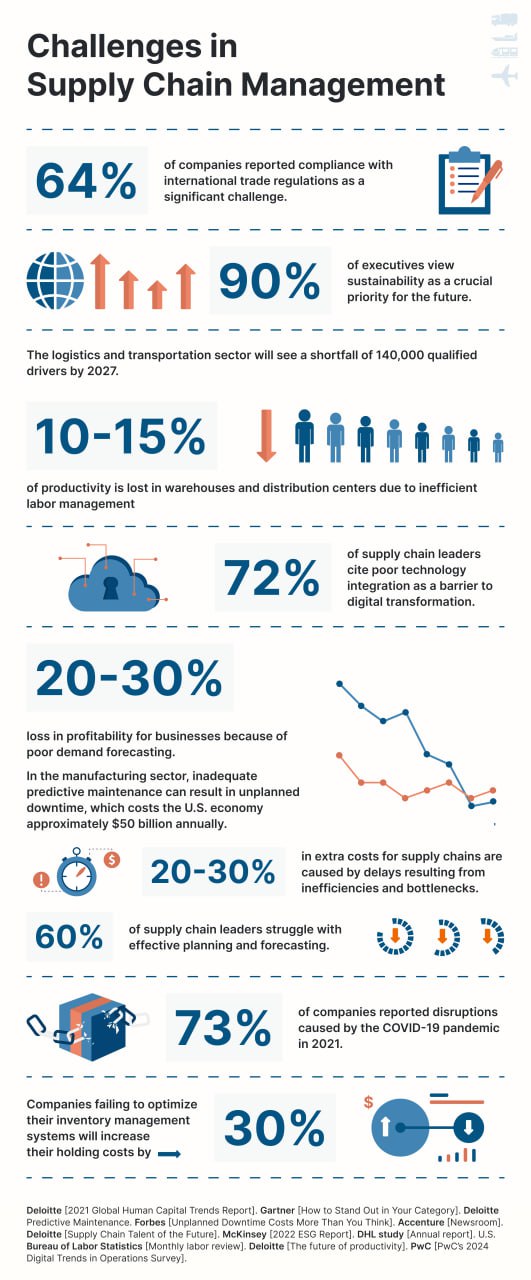
Today’s supply chains tend to grow into pretty complex structures, spawning tons of managerial, administrative, and compliance challenges. Most of these challenges stem from global disruptions, increasing operational costs, regulatory pressures, and the difficulty of integrating new technologies. Let’s take a look.
Supply chain disruptions
In 2021, nearly 73% of companies reported disruptions caused by the COVID-19 pandemic, according to Deloitte. Such disruptions have caused delays in production, transportation, and distribution, pushing businesses to rethink how they can build more resilient supply chains in the face of similar potential future disruptions.
In addition to pandemics, other factors like natural disasters and geopolitical tensions have strained supply lines across many corners of the world. The World Economic Forum (WEF) estimates that these disruptions have caused global trade to contract by 8.5% in 2020 alone, posing essential challenges to be prepared for today and in the future.
Rising Total Cost of Ownership (TCO)
Costs associated with supply chain operations are rising. From fuel prices to raw material shortages and increased labor costs, managing expenses has become more challenging. The regular supply chain’s TCO covers procurement, transportation, warehousing, and inventory costs. These growing costs can significantly impact profitability, especially for businesses that haven’t optimized their supply chain workflows.
According to the U.S. Bureau of Labor Statistics, the cost of logistics and transportation is rising by 19.6% each year in the US alone. On top of that, the Council of Supply Chain Management Professionals (CSCMP) reports that inventory carrying costs increased by over 25%, forcing companies to balance rising expenses and maintain competitiveness at the same time.
Demand & maintenance forecasting and accuracy
Accurately forecasting supply chain demand and maintenance needs is essential to maintaining a smooth logistical structure. Inaccurate predictions can result in overstocking, stockouts, and missed sales opportunities. Additionally, poor maintenance forecasting can provoke unexpected equipment breakdowns, further contributing to delays.
Deloitte estimates that poor demand forecasting leads to an average 20-30% loss in profitability for businesses. In the manufacturing sector, inadequate predictive maintenance can result in unplanned downtime, which costs the U.S. economy approximately $50 billion annually, Forbes reports.
The poor demand and maintenance forecasting challenge actually breaks down into two secondary issues:
- Lack of planning and forecasting
Effective planning is the backbone of a healthy supply chain. However, many companies still struggle with an inaccurate grip of their demand and inventory planning. It all stems from the lack of reliable data, which leads to inefficiencies that ripple across the entire supply chain, causing tons of challenges.
Deloitte survey found that 60% of supply chain leaders still struggle with effective planning and forecasting. Without reliable data, organizations either overestimate demand (excess inventory) or underestimate it (stockouts and lost sales).
- Bottlenecks
Bottlenecks in production, warehousing, or transportation can delay product delivery, making providers miss good business opportunities. Identifying and addressing bottlenecks requires a deep understanding of how all elements of the supply chain work together, something that can be difficult without the right technology and processes in place.
A recent study by Accenture found that inefficiencies caused by bottlenecks lead to delays, adding up to 20-30% in extra costs for supply chains. On the other hand, companies with well-equipped, technologically mature supply chains are 23% more profitable.
Sustainability and environmental concerns
Today’s consumers and regulators are demanding reduced carbon footprints, eco-friendly transportation, and as much sustainability implemented as possible. However, balancing these initiatives with cost efficiency presents a challenge.
According to a report by McKinsey, more than 90% of executives view sustainability as a crucial priority for the future. However, again, this sustainability must be balanced with overall profitability. Transportation alone accounts for 29% of U.S. greenhouse gas emissions, and regulatory pressure is mounting for businesses to lower their carbon footprint.
An inability to achieve a high level of sustainability in one’s supply chain leads to yet another essential issue:
- Regulatory and compliance issues
Global supply chains must operate under multiple layers of regulation, spanning different countries and regions. Keeping up with changing compliance standards, trade regulations, and customs procedures can be difficult and expensive. In a DHL study, 64% of companies reported compliance with international trade regulations as a significant challenge.
Technology integration
Technologically outdated legacy systems remain at the core of numerous businesses’ supply chain operations. Outdated software is difficult to integrate with new solutions, and it also tends to gather siloed data, slow down operations, and spawn more operational difficulties.
Organizations must adopt technology that can seamlessly integrate with their existing systems to stay competitive. A PwC survey showed that 72% of supply chain leaders cite poor technology integration as a barrier to digital transformation.
Inventory & warehouse management complexity
Poor inventory tracking, stock allocation, and replenishment inefficiency make companies lose profits. Warehouse management complexity is also exacerbated by the need for faster shipping and customer demands for near-instant gratification.
Gartner predicts that companies failing to optimize their inventory management systems will increase their holding costs by 30%. Mismanaged stock levels lead to underutilized space, overstocking, or stockouts, causing losses both in time and money.
Lack of personnel, labor costs, and inefficient employee management
Last but not least, a shortage of skilled labor, rising wages, and inefficient employee management contribute to higher operating costs. Furthermore, the automation of tasks like order fulfillment and warehouse operations has left gaps in employee training and productivity.
According to the U.S. Bureau of Labor Statistics, the logistics and transportation sector will see a shortfall of 140,000 qualified drivers by 2027. A Deloitte study found that inefficient labor management contributes to a 10-15% loss in productivity across warehouses and distribution centers.
Finding the Solution: Which Technologies Back Up Efficient Supply Chains?
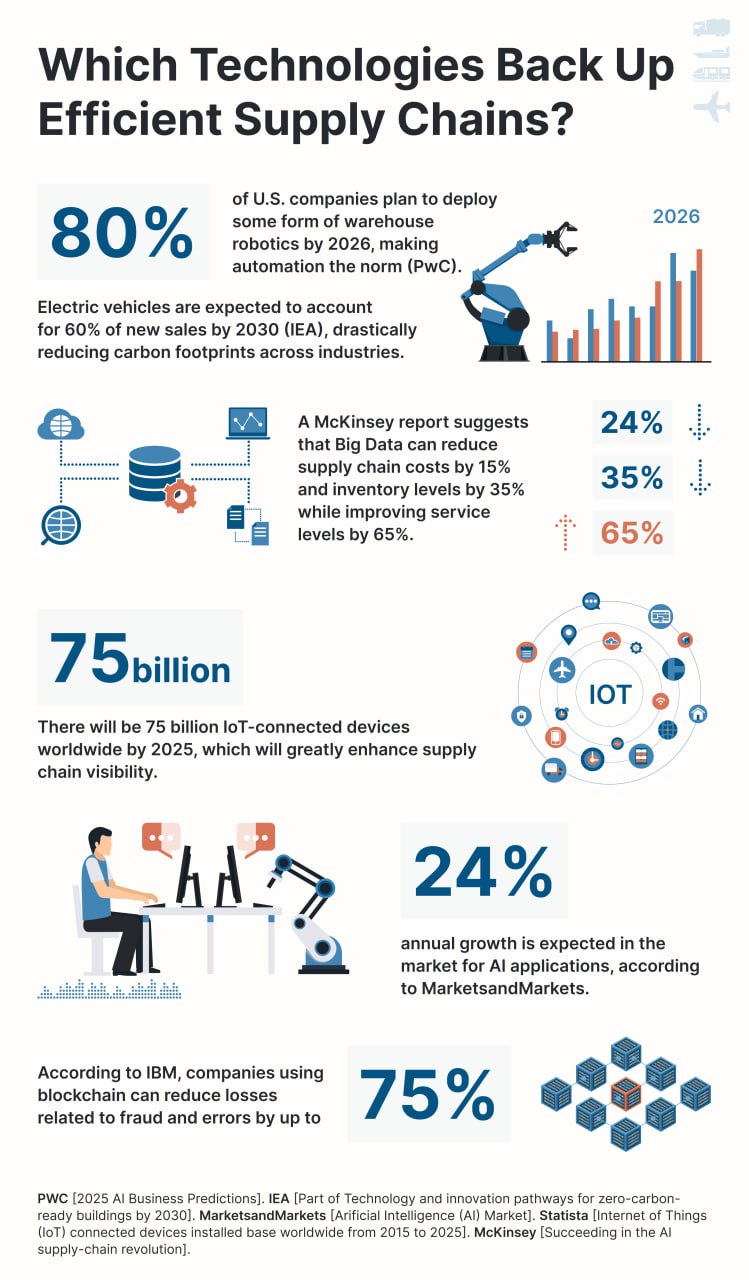
In response to all the abovementioned challenges, several key technology trends drive the future of supply chain management, helping organizations improve efficiency, reduce costs, and increase agility.
IoT to boost supply chain visibility
The Internet of Things allows organizations to set up interconnected, accessible networks of devices (e.g., truck/warehouse sensors), tracked objects (e.g., trucks), and software (e.g., digital endpoints), all of which can be monitored in real time. A Statista report predicts that there will be 75 billion IoT-connected devices worldwide by 2025, which will greatly enhance supply chain visibility.
Smart sensors attached to shipments can provide critical data on location, temperature, humidity, and condition, giving businesses greater visibility and control over their supply chains.
AI for prediction and telematics
The market for AI applications is expected to grow by 24% annually, according to MarketsandMarkets. Artificial intelligence (AI) reinvents supply chain management, route optimization, and machinery maintenance through predictive analytics and telematics. Telematics further enhances logistics by enabling the autonomous tracking of fleet performance and driver behavior, reducing transportation costs and improving delivery timelines.
Robotics, vehicle electrification, warehouse automation, and autonomous vehicles
Routine task and process automation is a competitive must these days. For warehouses, specialized robots can handle repetitive tasks like picking and packing. Many companies are also considering long-haul autonomous vehicles. Meanwhile, vehicle electrification helps reduce carbon emissions, improving sustainability in the supply chain.
Warehouse automation is becoming the norm, with 80% of U.S. companies planning to deploy some form of robotics by 2026 (PwC). Electric vehicles are expected to account for 60% of new sales by 2030 (IEA), drastically reducing carbon footprints across industries.
Big Data for predictive risk mitigation
Big data analytics is another key tool for mitigating risks in the supply chain. By analyzing large data sets, businesses can identify potential risks, such as supplier shortages or delivery delays, before they occur. Predictive analytics can also help companies optimize inventory levels and adjust procurement strategies to avoid disruptions.
A McKinsey report suggests that Big Data can reduce supply chain costs by 15% and inventory levels by 35% while improving service levels by 65%.
Blockchain for security and transparency
With decentralized blockchain ledgers, companies can track the journey of goods from production to delivery, ensuring data integrity and eliminating the risk of fraud. Blockchain can also help verify compliance with regulatory standards and improve collaboration across the supply chain network.
According to IBM, companies using blockchain can reduce losses related to fraud and errors by up to 75%.
Going for Specifics: Solutions to Overcome Supply Chain Challenges
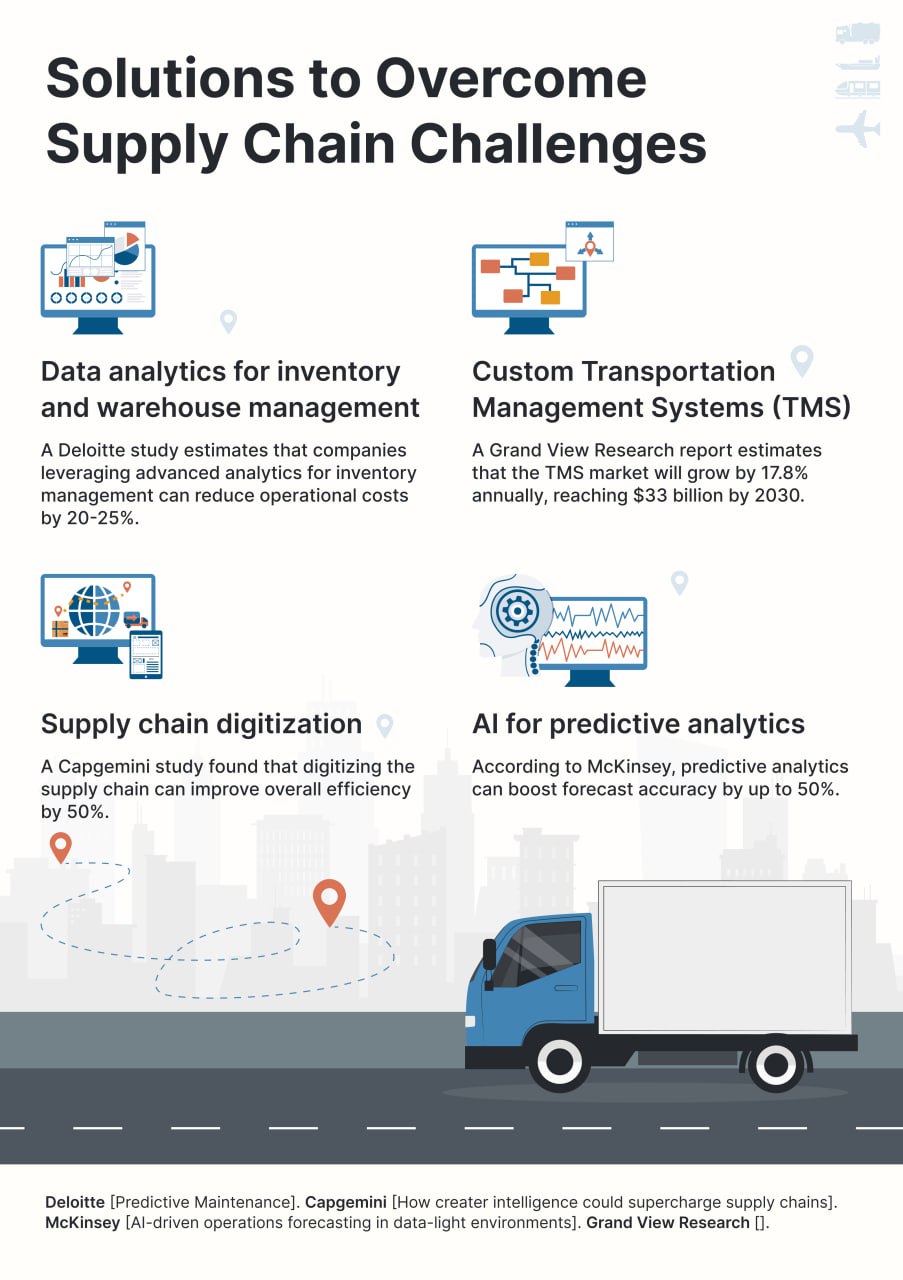
To overcome the abovementioned challenges and employ the trendiest technologies, companies must adopt up-to-date, technology-driven solutions that enable agility, resilience, and efficiency. These include the following.
Custom Transportation Management Systems (TMS)
A Grand View Research report estimates that the TMS market will grow by 17.8% annually, reaching $33 billion by 2030. Custom Transportation Management Systems are all-in-one route tracking, management, and optimization platforms that tie things up and streamline interactions.
TMS software allows organizations to manage the flow of goods more effectively, minimize transportation costs, and improve delivery performance by using data-driven insights to make informed decisions.
Supply chain digitization
A Capgemini study found that digitizing the supply chain can improve overall efficiency by 50%. From automated procurement processes to real-time inventory management, digitization brings transparency and efficiency to the supply chain, cutting out human error and manual tasks.
For instance, at IDAP, we had the pleasure of working on an all-in-one mobile app for the maintenance and repair tracking of trucks and truck fleets — Help My Truck. It is a specialized solution for truckers and supply chain companies running hauls across the USA, Canada, and Mexico.
Solutions like Help My Truck can be used by all supply chain participants to get a quick visual of the truck, communicate, adjust payments, and organize workflows throughout.
AI for predictive analytics
AI-powered predictive analytics allow businesses to gain deeper insights into demand patterns, fine-tune inventory management, and proactively address potential disruptions. By leveraging past performance data alongside current market trends, companies can enhance decision-making across procurement, production, and distribution processes.
This results in more precise forecasting, reduced excess inventory, and productive operations, ultimately boosting supply chain efficiency and reliability. According to McKinsey, predictive analytics can boost forecast accuracy by up to 50%.
Data analytics for inventory and warehouse management
A Deloitte study estimates that companies leveraging advanced analytics for inventory management can reduce operational costs by 20-25%. By using advanced analytics algorithms, businesses can improve stock allocation, optimize storage space, and smooth out the order fulfillment process, cutting out loads of expensive waste.
Summary
The challenges facing modern supply chains are complex and multifaceted, but they also present opportunities for growth and innovation. By adopting the latest technologies — such as IoT, AI, robotics, and blockchain — companies can improve supply chain visibility, optimize operations, and enhance sustainability efforts.
At IDAP, we have been building custom solutions for transportation management and supply chain digitization applied across all relevant industries, by all sorts of organizations and providers. We will help you embrace technology and innovation to thrive in this increasingly competitive market.
Feel free to contact us for details.